How to improve the space utilization of cylindrical battery pack?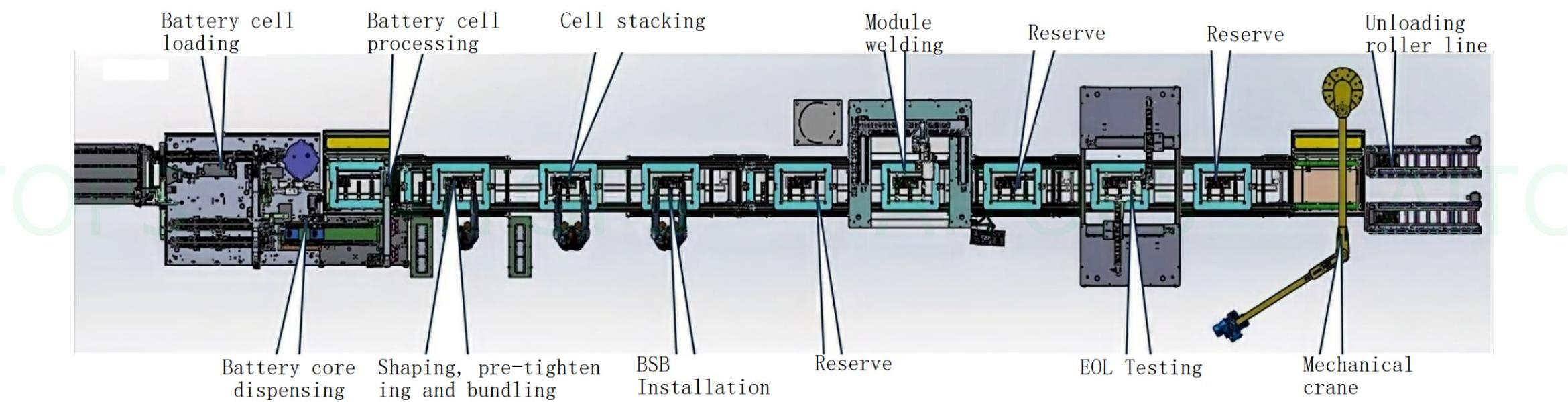
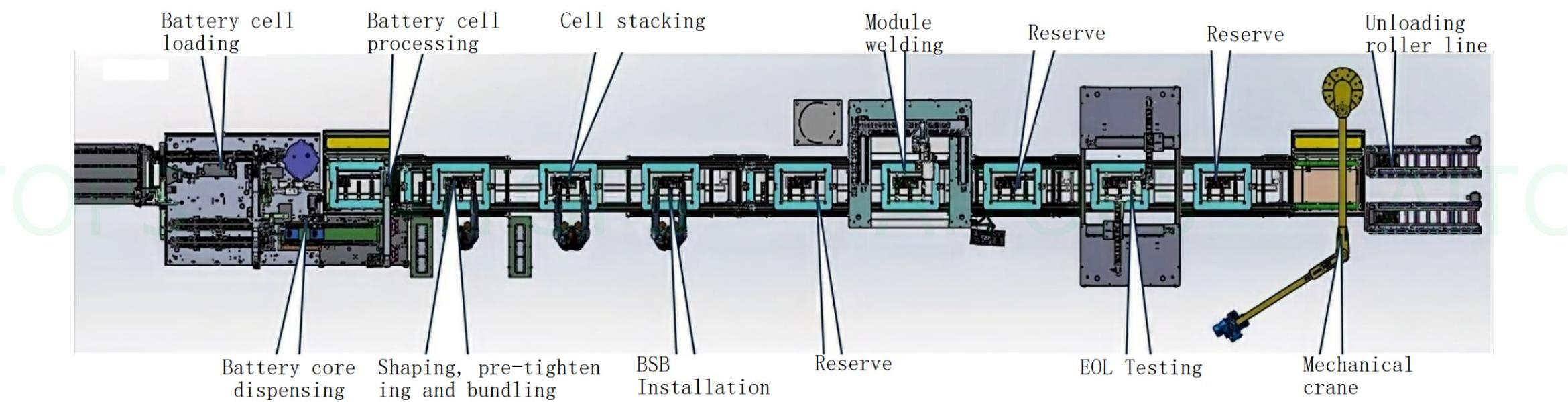
Improving the space utilization of cylindrical cell PACK can start from optimizing the arrangement, innovative structural design, and selecting appropriate cells and components.
1. Optimize arrangement
Adopt compact arrangement: Break through the traditional arrangement of rows and columns and adopt a tighter honeycomb arrangement. In the honeycomb arrangement, each cylindrical cell is in close contact with the surrounding cells, which can significantly reduce the gaps between cells compared to the conventional square array arrangement. Through this arrangement, space utilization can theoretically be increased by 10% - 15%.
Precise positioning and spacing control: With the help of high-precision molds and positioning tooling, it is ensured that each cylindrical battery cell can be accurately placed during the PACK process, and the spacing between battery cells is strictly controlled. Through advanced automation equipment and visual recognition systems, the cell spacing error is controlled within a very small range to maximize the use of space.
2. Innovative structural design
Integrated module design: Abandon the complex and space-consuming frame structure of traditional modules and adopt an integrated cast aluminum or injection molded module shell. This kind of shell can not only provide reliable physical protection for the battery core, but also directly serve as a heat dissipation channel and electrical connection carrier, reducing the space occupied by additional structural parts and making the internal space layout of the module more compact.
Flat design: On the premise of meeting the electrical performance and heat dissipation requirements, the overall height of the cylindrical battery pack is reduced as much as possible. For example, by optimizing the layout of the battery management system (BMS) circuit board, designing it into an ultra-thin and flexible form, it is placed on the side or bottom of the battery module instead of the traditional top placement, thereby effectively reducing the overall package cost. The height improves the installation adaptability in a specific space.
Multifunctional integrated structure: Design integrated structural components with multiple functions, such as integrating battery cell fixation, electrical connection and heat dissipation functions on the same component. This not only reduces the number of parts, but also avoids waste of space due to assembly relationships between components, improving overall space utilization.
3. Select appropriate batteries and components
Adaptable size battery cells: Select a cylindrical battery cell with appropriate diameter and height according to specific application scenarios and space constraints. For example, in some ultra-thin devices that have strict thickness requirements, using cylindrical cells with smaller diameters but relatively higher heights can better meet space requirements and improve space utilization.
Miniaturized components: Use miniaturized, highly integrated electronic components and connection components. For example, using miniaturized fuses, relays and flat cable connections, these miniaturized components can significantly reduce the space occupied inside the PACK while ensuring electrical performance.
4. Optimize thermal management system
Compact thermal management design: using micro-channel cooling technology or phase change material (PCM) combined with air cooling. The microchannel cooling plate can be designed to be very thin and fit the surface of the battery core. The phase change material can absorb heat while maintaining a relatively stable shape. Both of these methods can effectively manage heat while reducing the footprint of the thermal management system. space.
Shared space design: Integrate the thermal management system with the battery cell’s fixed structure or electrical connection structure. For example, the cooling ducts are combined with the support frame of the battery module, so that the thermal management system not only realizes the heat dissipation function, but also assumes the role of structural support, thereby improving space utilization.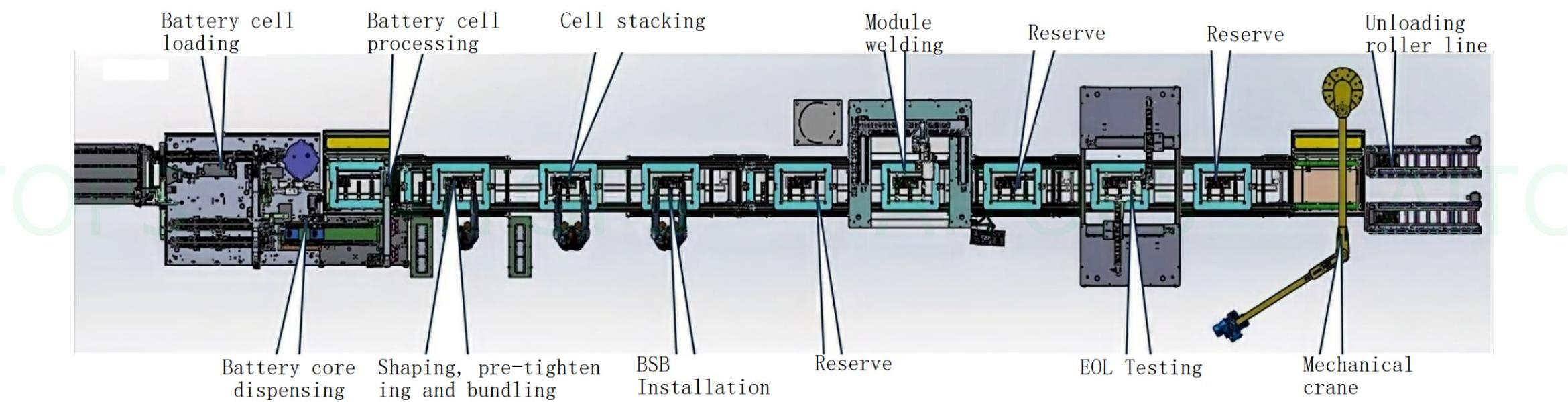
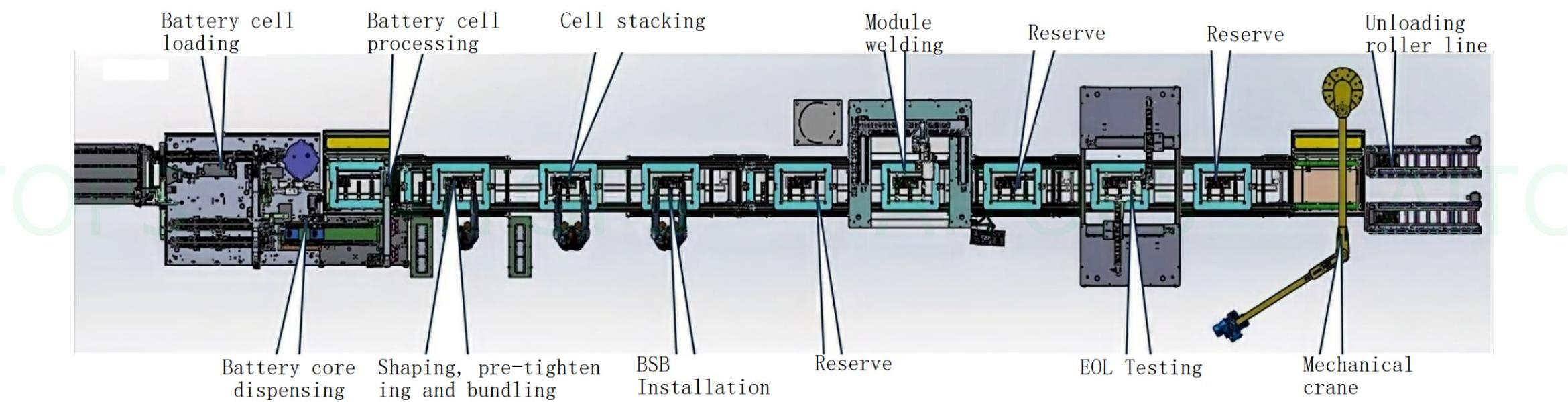